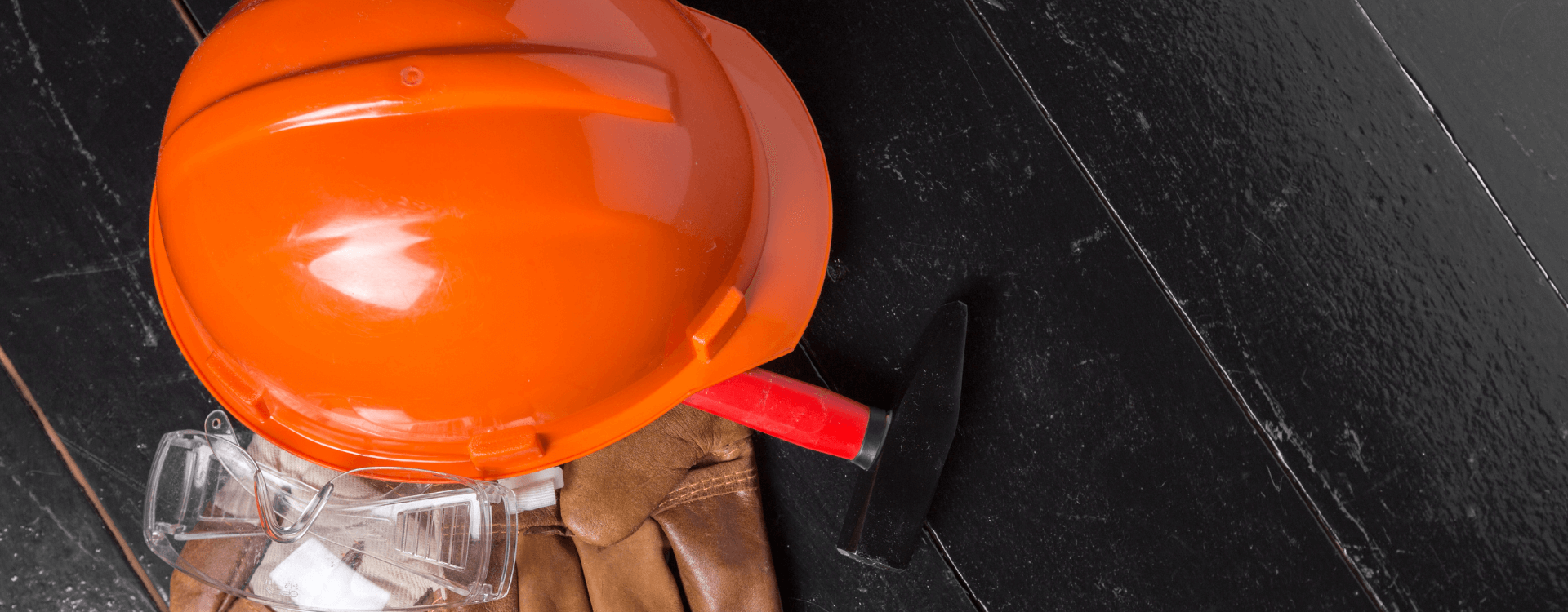
Safety at work and prevention : 5 good practices for your workshop
You remember perfectly your last accident at work. A bad cut on your thumb, because you neglected to wear gloves. You knew the tool and the manoeuvre to be performed. However, what was supposed to last 5 minutes ended up in the emergency room, in a bloodbath, with the impossibility of doing any mechanical work for several weeks. Since this event, you are aware that things need to be changed and, above all, the mentality within the workshop. Safety at work and the prevention of occupational risks are a daily battle that concerns all the employees of your garage, whether they are in the offices or at the nail box. Here are a few good practices to put in place right away.
Benefit from EXCEPTIONAL ADVANTAGES reserved for PROs!
BP #1 embed good practice in the company culture
An alarming finding
A car garage alone groups together the main risks in the sector of activity: falls from a height, falls from a level, musculoskeletal disorders (MSD) and chemical risk. According to the report drawn up by the Assurance Maladie in December 2020, 88% of occupational illnesses are related to MSD and this figure is constantly increasing. Absenteeism due to accidents is costly for companies, reduces productivity and completely disorganises teams.
More concretely, it forces you to increase the waiting time for your customers or to resort to interim staff. This solution is all the more costly as its real effectiveness is only felt after several weeks, the time it takes for the new recruit to be fully trained in your working methods.
The need to change minds
The solution to accidents lies partly in two words, awareness and prevention. Even if you can't predict the unpredictable, you can still mitigate the effects of chance. It all starts with your attitude and with the impetus you give to your mechanics and employees. It is up to you to show that wearing PPE is essential and does not tolerate any exceptions. But you can't change people's minds at the snap of a finger. Don't hesitate to involve your mechanics, for example by asking them to identify the hazards specific to each machine and each sector of the workshop. Then establish the correct actions to be taken and the mandatory equipment for each. Adherence is more natural and sustainable when it comes from the workers themselves. Safety rules are first and foremost common sense and are designed for the benefit of all.
BP #2 Give a proper welcome to newcomers
Newcomers, especially if they are young and just out of training school, must be made aware of the (good) habits of your garage. You must therefore welcome them by reminding them or teaching them the good practices in force.
Young mechanics receive solid training in occupational safety at school. They already have their feet on the ground, so it's up to you to continue this.
The Auto Prévention site is offering garage owners a free download of the welcome kit for new workers. It contains a series of documents for training newcomers in workplace prevention and safety. This tool is a comprehensive method of increasing your efficiency, profitability and, most importantly, your credibility with your employees.
BP #3 Confront the problem by assessing the risks
When it comes to safety at work, good intentions are not enough, only concrete actions count. Yes, but how to proceed methodically and effectively ?
The DUER
The Single Risk Assessment Document is compulsory as soon as the first employee is hired, regardless of the sector of activity and the size of the company. Thanks to this guide document, you assess, identify and classify the risks and dangers. You can then propose the appropriate preventive actions.
This document must be available for consultation by all, updated every year and kept at the disposal of the Labour Inspectorate. Failure to comply with any of these obligations is punishable by a fine.
The OIRA tool
The OIRA (Online Interactive Risk Assessment) is an interactive online risk assessment tool. It is one of the ways to map all the risks present in the company and to determine whether they are under control or not.
All you have to do is register your car garage in the application and select your sector of activity. Then just let yourself be guided and complete each section. This assessment takes time, you can absolutely carry it out in several working sessions. Once all the elements have been filled in, you will have a complete risk assessment document.
BP #4 Workplace safety and prevention : review your internal organisation
A safe workspace is tidy and well organised. This sounds obvious to write and read, but in reality it is a bit more complex. So why not apply the good old principles of lean management ? Very often, companies in the logistics sector have applied the 5 S method, borrowed from the Toyota group.
Seiri (delete)
The initial step is of course to sort out, throw away or recycle what can be recycled. You only keep what is related to your field of activity and therefore not useful. It is certain that you will not arouse delirious enthusiasm by proposing this spring cleaning. It is up to you to involve your employees in this process by relying on those who are most motivated by this approach. It often only takes a small spark to set the whole workshop alight. Figuratively speaking, of course.
Seiton (locate)
Now that the sorting stage is done, it is time to put away and put back what needs to be put away. Make mechanics aware that tools should be put in their place and that equipment should not be moved around the workshop unnecessarily. The benefit of this is obvious : mechanics no longer waste time chasing a tool and the risk of losing them is greatly reduced.
Some workstations can also be moved. While the location of the lift is set in stone, so to speak, this is not the case for all. Noisy equipment such as compressors or pneumatic tools should be placed in a way that limits noise pollution. This can be in a soundproof room or protected by a sound barrier.
Seiso (cleaning)
Cleaning is easier if the first two steps have been done well. A clean workspace is much more pleasant and contributes to well-being at work. The current pandemic is not going to contradict us on this point.
Well-maintained and well-oiled tools and equipment greatly reduce the risk of accidents. It makes them easier to handle. In addition to improving the safety of your teams, you also improve their performance.
Seiketsu (standardize)
Tidiness and cleanliness are not optional, but should become automatic for everyone, at all levels. All these recommendations are of course valid for all your departments and do not only concern the workshop. The offices and reception area must also be cleaned and sorted.
Shitsuke (follow)
One of the advantages of the 5S method is that the benefits are immediately visible. The cleaning and reorganisation of the premises has most likely brought your employees together in this joint effort. Everyone can't help but recognise the benefits of growing and working in a healthier environment. Order and cleanliness will reign for several weeks or months until human nature takes over again. Implementing the first four steps takes time, but we guarantee that it will take much less time for the old situation to return. Therefore, careful monitoring is essential.
BP #5 Invest in better equipment
Your assessment has probably highlighted the obsolescence of certain equipment. It is high time to consider some investments for the well-being of your employees. Health insurance promotes a program, TMS Pro Action. This is a subsidy reserved for companies with fewer than 50 employees to support them in the purchase or renewal of equipment designed to reduce the physical strain on workers, particularly when handling loads. The grant is between €2 000 and €25 000 and you can apply for it on the website net-entreprises.
Image sources:
Marie CHASLES / Author: Catalin Pop / License ID: #112018263 - stock.adobe.com